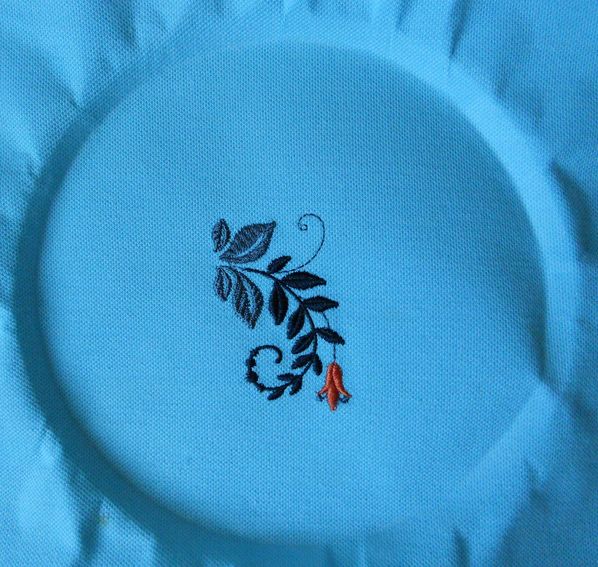
Introduction
Welcome to the world of machine embroidery, where creativity meets precision. As embroidery enthusiasts and professionals, we've all experienced the excitement of completing a beautiful design, only to be met with the frustration of hoop burn. This common issue can turn a masterpiece into a mishap in seconds. But fear not! In this comprehensive guide, we'll delve into the intricacies of hoop burn, exploring its causes, prevention methods, and innovative solutions. Whether you're a seasoned pro or just starting your embroidery journey, this article will equip you with the knowledge and techniques to keep your projects flawless and your fabrics pristine.
2. Understanding Hoop Burn in Machine Embroidery
2.1 What is Hoop Burn?
Hoop burn, the bane of embroiderers worldwide, is a frustrating phenomenon that can turn your meticulously crafted masterpiece into a disappointing disaster. But what exactly is this embroidery nemesis?
Hoop burn refers to the visible marks or indentations left on fabric after it has been tightly secured in an embroidery hoop. These marks often appear as shiny, compressed areas that outline the shape of the hoop, marring the overall appearance of your finished project. Imagine the disappointment of removing a beautifully stitched design from the hoop, only to find an unsightly ring surrounding your work!
This issue occurs when the fabric fibers are compressed and distorted due to the pressure exerted by the embroidery hoop. The result? A telltale circular or oval imprint that can be stubborn to remove, particularly on delicate or pile fabrics.
2.2 Common Causes of Hoop Burn
Understanding the root causes of hoop burn is crucial for prevention. Let's dive into the main culprits:
-
Overtightening the Hoop:
The most common cause of hoop burn is excessive tension when securing the fabric in the hoop. It's tempting to tighten the hoop as much as possible to prevent slippage, but this can lead to severe compression of the fabric fibers. -
Extended Hooping Time:
Leaving fabric in the hoop for prolonged periods, especially overnight, can exacerbate the risk of hoop burn. The longer the fabric remains under pressure, the more likely it is to develop permanent marks. -
Inappropriate Hoop Size:
Using a hoop that's too small for your design can necessitate multiple re-hoopings, increasing the risk of hoop burn with each adjustment. -
Fabric Characteristics:
Some fabrics are more susceptible to hoop burn due to their composition or texture. Delicate fabrics like silk or velvet, and those with a high pile, are particularly vulnerable. -
Incorrect Hooping Technique:
Improper hooping methods, such as stretching the fabric too tightly or unevenly, can lead to localized areas of intense pressure and subsequent burn marks. -
Heat and Moisture:
The combination of heat from the embroidery machine and moisture (either from the environment or the fabric itself) can intensify the effects of hoop burn, making the marks more pronounced and difficult to remove.
2.3 Fabrics Most Susceptible to Hoop Burn
Not all fabrics are created equal when it comes to hoop burn resistance. Some materials are particularly prone to this embroidery woe:
-
Velvet and Velveteen:
The delicate pile of these luxurious fabrics is easily crushed, leaving visible marks that can be challenging to restore. -
Silk and Satin:
These smooth, glossy fabrics show even the slightest pressure marks, making them highly susceptible to hoop burn. -
Knits and Stretchy Fabrics:
The elasticity of these materials makes them prone to distortion when hooped tightly, often resulting in visible marks. -
Microfiber and Synthetic Blends:
These fabrics can "melt" slightly under pressure and heat, leading to shiny, permanent marks. -
Terry Cloth and Towels:
The looped pile of these fabrics can be easily flattened, creating noticeable hoop marks. -
Corduroy and Ribbed Fabrics:
The raised texture of these materials makes them particularly vulnerable to compression marks. -
Leather and Suede:
While not traditional embroidery fabrics, these materials can show permanent indentations from hooping. -
Delicate Natural Fibers:
Fabrics like linen and fine cotton can also show hoop marks, especially when embroidered with dense designs.
Understanding these fabric sensitivities is crucial for embroiderers. It allows you to take preemptive measures, such as using alternative hooping methods or selecting more appropriate stabilizers.
For those working with these challenging fabrics, consider exploring innovative solutions like MaggieFrame's magnetic embroidery hoops. These hoops offer a gentler grip on delicate materials, significantly reducing the risk of hoop burn across various fabric types. Their universal compatibility and improved efficiency make them an excellent choice for both professional embroiderers and enthusiasts alike.
By recognizing what hoop burn is, understanding its causes, and identifying susceptible fabrics, you're well on your way to mastering the art of hoop burn prevention. Remember, the key to flawless embroidery lies not just in your stitching skills, but also in your ability to handle and prepare your fabric with care and precision.
3. Preventing Hoop Burn
In the world of machine embroidery, preventing hoop burn is just as crucial as creating beautiful designs. Let's dive into the most effective techniques to keep your fabrics pristine and your embroidery flawless.
3.1 Proper Hooping Techniques
Mastering the art of hooping is your first line of defense against hoop burn. Here are some expert tips to ensure you're hooping like a pro:
- Find the Sweet Spot: Tension is key, but finding the right balance can be tricky. Your fabric should be drum-tight, but not stretched to the point of distortion. Think of it as tuning a guitar string - too loose and it wobbles, too tight and it snaps.
- The Sandwich Method: Layer your fabric between stabilizer sheets. This not only provides extra support but also acts as a buffer between the fabric and the hoop's edges.
- Center Perfection: Always center your fabric in the hoop. Uneven distribution of tension is a fast track to hoop burn.
- Size Matters: Use the appropriate hoop size for your design. A hoop that's too small forces you to rehoop multiple times, increasing the risk of burn marks.
- The Finger Test: After hooping, run your finger along the inside edge of the hoop. If you feel ridges or puckers, it's time to adjust.
- Loosen Up: When you're done embroidering, loosen the hoop immediately. Leaving fabric tightly hooped for extended periods is like asking for hoop burn.
- The Clock Method: When tightening your hoop, work your way around it like the face of a clock. This ensures even tension all the way around.
By implementing these techniques, you'll significantly reduce the risk of hoop burn. Remember, practice makes perfect, and over time, proper hooping will become second nature.
3.2 Using the Right Stabilizers
Stabilizers are the unsung heroes of embroidery, playing a crucial role in preventing hoop burn. Let's explore how to choose and use them effectively:
-
Know Your Fabrics: Different fabrics require different stabilizers. Here's a quick guide:
- Light fabrics (silk, organza): Use light, tear-away stabilizers
- Medium fabrics (cotton, linen): Opt for medium-weight cut-away or tear-away
- Heavy fabrics (denim, canvas): Choose heavy-weight cut-away stabilizers
-
Layer Up: Don't be afraid to use multiple layers of stabilizer for extra protection against hoop burn. It's better to have too much stabilizer than too little.
-
Adhesive Stabilizers: These can be a game-changer for difficult fabrics. They hold the fabric in place without excessive hooping pressure.
-
Water-Soluble Stabilizers: Perfect for delicate fabrics or projects where you don't want any stabilizer visible after washing.
-
Fusible Stabilizers: These bond to the fabric with heat, providing extra stability without the need for tight hooping.
-
Floating Technique: For fabrics prone to hoop burn, try floating. Hoop only the stabilizer and secure the fabric to it with temporary adhesive spray.
-
Stabilizer Placement: Always place stabilizer between the fabric and the hoop. This creates a buffer zone, reducing direct pressure on the fabric.
-
Test, Test, Test: Before embarking on your main project, always do a test run with your chosen stabilizer and fabric combination.
Remember, the right stabilizer not only prevents hoop burn but also improves the overall quality of your embroidery. It's worth investing time to find the perfect match for each project.
3.3 Adjusting Machine Settings
Fine-tuning your embroidery machine settings can make a world of difference in preventing hoop burn. Let's explore how to optimize your machine for burn-free embroidery:
- Tension Matters: Proper thread tension is crucial. Too tight, and you risk puckering the fabric; too loose, and your design may not hold up. Find that sweet spot where the top and bottom threads meet in the middle of the fabric.
- Speed Control: Slower isn't always better, but for delicate fabrics or intricate designs, reducing your machine's speed can help prevent fabric distortion and subsequent hoop burn.
- Needle Selection: Choose the right needle for your fabric. A needle that's too large can leave visible holes, while one that's too small may not penetrate properly, causing the fabric to pull and potentially burn.
- Stitch Density: Adjust your design's stitch density based on the fabric. Lighter fabrics require less dense stitching to prevent puckering and potential burn marks.
- Underlay Stitches: Use appropriate underlay stitches to stabilize the fabric before the main design. This can reduce fabric movement and the need for overly tight hooping.
- Presser Foot Pressure: If your machine allows, adjust the presser foot pressure. Less pressure can be gentler on delicate fabrics.
- Hoop Attachment: Ensure your hoop is securely attached to the machine. A loose hoop can cause unnecessary movement and friction.
- Design Placement: Center your design within the hoop. This distributes tension evenly and reduces the risk of hoop burn at the edges.
- Software Settings: If you're digitizing your own designs, use your software to optimize stitch direction and pull compensation, reducing fabric distortion.
- Regular Maintenance: Keep your machine clean and well-oiled. A smooth-running machine is less likely to cause fabric issues.
By fine-tuning these settings, you're not just preventing hoop burn; you're setting the stage for professional-quality embroidery. Remember, every fabric and design may require slightly different settings, so don't be afraid to experiment and keep notes on what works best.
3.4 MaggieFrame Magnetic Hoops: A Solution to Prevent Hoop Burn
In the quest for burn-free embroidery, innovative solutions like MaggieFrame's magnetic hoops have emerged as game-changers. Let's explore how these advanced hoops are revolutionizing the way we approach hoop burn prevention:
- Gentle Yet Secure Hold: MaggieFrame's magnetic system provides a firm grip without the excessive pressure of traditional hoops. This significantly reduces the risk of hoop burn, especially on delicate fabrics.
- Even Tension Distribution: The magnetic force is distributed evenly around the hoop, eliminating hot spots that can lead to burn marks.
- Quick Release: Unlike traditional hoops that require loosening screws, magnetic hoops allow for instant release. This means less time under tension for your fabric, further reducing burn risk.
- Versatility: MaggieFrame hoops are compatible with a wide range of embroidery machines, making them a versatile solution for both home enthusiasts and professional embroiderers.
- Reduced Fabric Distortion: The unique design of these hoops minimizes fabric stretching, helping maintain the integrity of your material throughout the embroidery process.
- Easy Repositioning: Need to adjust your fabric? Magnetic hoops allow for quick and easy repositioning without the risk of creating new pressure points.
- Time-Saving: The ease of use not only prevents hoop burn but also speeds up your workflow, allowing for more efficient production without compromising quality.
- Durability: MaggieFrame hoops are built to last, offering a long-term solution to hoop burn prevention that pays for itself over time.
- Ideal for Challenging Fabrics: These hoops excel with fabrics that are traditionally difficult to hoop, such as stretchy knits or slippery silks.
- User-Friendly Design: Even beginners can achieve professional-level hooping with these intuitive magnetic systems, reducing the learning curve and the risk of mistakes that lead to hoop burn.
By incorporating MaggieFrame magnetic hoops into your embroidery toolkit, you're not just preventing hoop burn; you're elevating your entire embroidery experience. These innovative hoops offer a perfect blend of technology and practicality, ensuring your projects remain burn-free while streamlining your workflow.
Remember, while MaggieFrame hoops are an excellent tool, they work best when combined with proper technique and understanding of your materials. Always consider the specific needs of your project and fabric when choosing your hooping method.
4. Identifying Hoop Burn
In the world of machine embroidery, hoop burn can be a frustrating obstacle to achieving perfect results. Recognizing the signs of hoop burn and distinguishing it from other fabric issues is crucial for maintaining the quality of your embroidery projects. Let's delve into the telltale signs of hoop burn and how to differentiate it from other common fabric problems.
4.1 Visual Signs of Hoop Burn
Hoop burn leaves distinct marks on your fabric that can be easily identified once you know what to look for. Here are the key visual indicators:
- Circular or Oval Impressions: The most obvious sign of hoop burn is a visible outline that matches the shape of your embroidery hoop. This impression often appears as a shiny, compressed ring around your embroidered design.
- Flattened Fibers: In fabrics with pile or texture, such as velvet or terry cloth, hoop burn manifests as a noticeable flattening of the fibers in the affected area.
- Shiny Marks: On smooth fabrics like silk or satin, hoop burn often appears as a glossy or shiny mark where the hoop compressed the fabric.
- Color Changes: In some cases, particularly with darker fabrics, the area affected by hoop burn may appear lighter or have a slightly different hue than the surrounding fabric.
- Visible Hoop Lines: You might notice distinct lines that correspond to the inner and outer edges of your embroidery hoop, especially on delicate or light-colored fabrics.
- Fabric Distortion: In severe cases, hoop burn can cause the fabric to become permanently stretched or distorted in the shape of the hoop.
- Texture Changes: Even if the color remains unchanged, you might feel a difference in texture where the hoop was placed, with the affected area feeling smoother or more compressed.
By familiarizing yourself with these visual cues, you'll be better equipped to identify hoop burn quickly and take appropriate action to prevent or remedy it.
4.2 Differentiating Hoop Burn from Other Fabric Issues
While hoop burn has its distinct characteristics, it can sometimes be confused with other fabric issues. Here's how to distinguish hoop burn from similar problems:
-
Hoop Burn vs. Water Marks:
- Hoop Burn: Follows the shape of the hoop, often circular or oval.
- Water Marks: Irregular shapes, often with a "tide line" effect.
-
Hoop Burn vs. Heat Damage:
- Hoop Burn: Typically doesn't change the fabric's structure, just compresses it.
- Heat Damage: Can melt or scorch fibers, leaving permanent discoloration or holes.
-
Hoop Burn vs. Stabilizer Residue:
- Hoop Burn: Affects the fabric's texture and appearance.
- Stabilizer Residue: Leaves a stiff or papery feeling, often with visible flakes or film.
-
Hoop Burn vs. Fabric Puckering:
- Hoop Burn: Creates a flat, compressed area.
- Puckering: Causes fabric to bunch up or create small folds around the embroidery.
-
Hoop Burn vs. Tension Issues:
- Hoop Burn: Affects the fabric outside the embroidered area.
- Tension Issues: Primarily impact the embroidered design itself, causing loose stitches or pulls.
-
Hoop Burn vs. Needle Holes:
- Hoop Burn: Covers a larger area, often in a ring shape.
- Needle Holes: Small, individual punctures in the fabric, usually within the embroidered area.
To accurately identify hoop burn, consider the following:
- Location: Hoop burn typically appears around the embroidered design, not within it.
- Pattern: Look for a consistent pattern that matches your hoop's shape and size.
- Texture: Feel the fabric for changes in texture or compression.
- Reversibility: Unlike some other issues, hoop burn can often be remedied with proper treatment.
By understanding these distinctions, you can more confidently diagnose hoop burn and choose the appropriate solution. Remember, prevention is always better than cure. Consider using innovative tools like MaggieFrame's magnetic embroidery hoops, which offer a gentler grip on fabrics, significantly reducing the risk of hoop burn across various fabric types. Their universal compatibility and improved efficiency make them an excellent choice for both professional embroiderers and enthusiasts alike, helping to maintain the integrity of your fabrics while achieving flawless embroidery results.
5. Removing Hoop Burn
5.1 Immediate Actions After Discovering Hoop Burn
When you unveil your embroidery project only to discover the dreaded hoop burn, don't panic! Quick action can often save your work. Here's what to do immediately:
- Assess the Damage: Carefully examine the affected area. Is it a minor compression mark or a more severe burn?
- Don't Iron!: Resist the urge to iron the mark immediately. Heat can set the burn, making it harder to remove.
- Gently Manipulate the Fabric: Use your fingers to lightly rub the affected area in a circular motion. This can help relax the fibers and potentially reduce the visibility of the burn.
- Allow Time to Relax: Sometimes, simply allowing the fabric to rest for a few hours can help the fibers bounce back naturally.
- Prepare for Treatment: If the burn persists, prepare to treat it using one of the methods we'll discuss next.
Remember, prevention is always better than cure. Consider using MaggieFrame's magnetic embroidery hoops for future projects. Their innovative design significantly reduces the risk of hoop burn, especially on delicate fabrics, while offering universal compatibility with various embroidery machines.
5.2 Wet Removal Methods
When it comes to removing hoop burn, wet methods can be surprisingly effective. Here are some techniques to try:
-
Water Spraying Technique:
- Fill a spray bottle with clean water.
- Lightly mist the affected area.
- Gently pat the fabric with your fingers.
- Allow to air dry completely.
-
Steam Treatment:
- Hold the fabric over a steaming kettle or use a handheld steamer.
- Keep the fabric about 6 inches away from the steam source.
- Move the fabric around to ensure even distribution of steam.
- After steaming, lay the fabric flat to dry.
-
Ice Cube Method:
- Gently rub an ice cube over the hoop burn.
- As the ice melts, it will slowly rehydrate the fabric fibers.
- Once the area is damp, use your fingers to gently massage the fabric.
- Allow to air dry naturally.
-
Damp Cloth Technique:
- Dampen a clean, white cloth with room temperature water.
- Place the cloth over the hoop burn.
- Gently press down, allowing the moisture to transfer to the fabric.
- Remove the cloth and let the area air dry.
Remember, different fabrics react differently to moisture. Always test these methods on an inconspicuous area first. For delicate or non-washable fabrics, proceed with extra caution or consider professional cleaning.
Pro Tip: MaggieFrame's magnetic hoops can help prevent hoop burn in the first place, reducing the need for these removal techniques. Their gentle yet secure hold minimizes fabric compression, making them an excellent choice for both professionals and hobbyists.
5.3 Dry Removal Methods
When wet methods aren't suitable or haven't been effective, try these dry techniques to remove hoop burn:
-
Lint Roller Technique:
- Use a clean lint roller or adhesive tape.
- Gently roll over the affected area.
- The adhesive helps lift and separate the compressed fibers.
- Repeat several times, rotating the roller for a clean surface each time.
-
Fabric Brushing:
- Use a soft-bristled brush (like a clean toothbrush or fabric brush).
- Gently brush the hoop burn area in circular motions.
- This helps to lift and separate the flattened fibers.
- For pile fabrics, brush in the direction of the nap.
-
Same-Fabric Rubbing:
- Find a scrap of the same fabric or an inconspicuous area of the garment.
- Rub this piece against the hoop burn area.
- The friction between identical fabrics can help restore the original texture.
-
Fingernail Method:
- Gently scratch the hoop burn area with your fingernail.
- Work in small sections, moving in different directions.
- This can help separate compressed fibers without damaging the fabric.
-
Fabric Shaver:
- For stubborn marks on pile fabrics, a fabric shaver can help.
- Very gently run the shaver over the affected area.
- This removes the flattened top layer, revealing the undamaged fibers beneath.
- Use with extreme caution to avoid damaging the fabric.
Remember, these methods work best on fresh hoop burns. For persistent marks, you may need to combine techniques or move on to chemical treatments.
Pro Tip: To minimize the need for these removal techniques, consider using MaggieFrame's magnetic embroidery hoops. Their innovative design distributes pressure more evenly, significantly reducing the risk of hoop burn across various fabric types.
5.4 Chemical Treatments
When mechanical methods fall short, chemical treatments can be a game-changer in removing stubborn hoop burn. However, always exercise caution and test on an inconspicuous area first.
-
Vinegar Solution Method:
- Mix equal parts white vinegar and water.
- Apply the solution to the burn mark using a clean cloth.
- Gently dab, don't rub.
- Allow to air dry, then assess the results.
- Repeat if necessary, but avoid oversaturating the fabric.
-
Fabric Conditioner Application:
- Dilute fabric conditioner with water (1:4 ratio).
- Apply the mixture to the hoop burn using a soft brush.
- Gently work it into the fibers.
- Rinse with clean water and air dry.
- This method works well for restoring softness to compressed fibers.
-
Commercial Hoop Burn Removers:
- Several products are specifically designed for hoop burn removal.
- Follow the manufacturer's instructions carefully.
- These often contain enzymes or other specialized ingredients.
- Be sure to choose a product suitable for your fabric type.
-
Mild Soap Solution:
- Mix a small amount of gentle, pH-neutral soap with water.
- Apply the solution with a soft cloth, dabbing gently.
- Rinse thoroughly with clean water to remove all soap residue.
- Air dry and assess the results.
-
Baking Soda Paste:
- Create a paste with baking soda and a small amount of water.
- Apply to the hoop burn area and let sit for 15-20 minutes.
- Gently brush off the dried paste.
- This can help absorb odors and lift light stains associated with hoop burn.
Remember, chemical treatments should be your last resort. They can be effective but also carry the risk of altering fabric color or texture if not used correctly.
Pro Tip: To minimize the need for chemical treatments, consider investing in high-quality hooping equipment. MaggieFrame's magnetic embroidery hoops, for instance, offer a gentle yet secure grip that significantly reduces the risk of hoop burn. Their innovative design is compatible with a wide range of embroidery machines, making them a versatile choice for both professionals and hobbyists.
5.5 Specialized Techniques for Different Fabrics
Different fabrics require tailored approaches when it comes to removing hoop burn. Here are some specialized techniques for various fabric types:
-
Delicate Fabrics (Silk, Chiffon, Organza):
- Use a fine mist of water and gently pat with fingertips.
- For silk, try the ice cube method, being extremely gentle.
- Avoid harsh chemicals or excessive rubbing.
-
Pile Fabrics (Velvet, Corduroy, Chenille):
- Steam treatment is often most effective.
- Use a soft-bristled brush to gently lift the pile.
- For velvet, try the "same-fabric rubbing" technique.
-
Knits and Stretchy Fabrics:
- Gently stretch the fabric perpendicular to the burn mark.
- Use the water spray method, allowing the fabric to air dry while stretched.
-
Synthetic Fabrics (Polyester, Nylon):
- Try the vinegar solution method.
- For stubborn marks, a fabric shaver can help, but use with extreme caution.
-
Natural Fibers (Cotton, Linen):
- The water spray or steam methods often work well.
- For tough cases, try the baking soda paste technique.
-
Leather and Suede:
- Use a suede brush or clean pencil eraser to gently lift the nap.
- For leather, try a specialized leather conditioner.
-
Denim and Heavy Fabrics:
- Steam treatment followed by brushing can be effective.
- For extreme cases, carefully use sandpaper to restore texture.
-
Embroidered Areas:
- Be extra cautious to avoid damaging the stitching.
- Gentle steaming often works best.
Remember, prevention is always better than cure. Consider using MaggieFrame's magnetic embroidery hoops, which are designed to minimize the risk of hoop burn across various fabric types. Their universal compatibility and improved efficiency make them an excellent choice for both professional embroiderers and enthusiasts alike.
Pro Tip: Always test your chosen method on an inconspicuous area first, and when in doubt, consult a professional cleaner, especially for valuable or delicate items.
6. Alternative Hooping Methods
In the quest for perfect embroidery, sometimes traditional hooping techniques fall short. This section explores innovative alternatives that can help you achieve flawless results, especially when dealing with challenging fabrics or intricate designs. Let's dive into these game-changing methods that can revolutionize your embroidery process.
6.1 Floating Technique
The floating technique is a versatile solution for embroidering items that are difficult or impossible to hoop traditionally. This method involves securing the stabilizer in the hoop and then attaching the fabric to the stabilizer, allowing it to "float" above the hoop.
6.1.1 When to Use the Floating Technique
- Embroidering on finished garments (e.g., collars, cuffs, pockets)
- Working with delicate or stretchy fabrics
- Embroidering small items or awkward areas
- Avoiding hoop marks on pile fabrics like velvet or terry cloth
6.1.2 Steps for Floating
- Hoop a piece of stabilizer appropriate for your project.
- Secure your fabric to the hooped stabilizer using one or more of these methods:
- Temporary adhesive spray
- Pins (placed outside the embroidery area)
- Basting stitches (either by machine or hand)
- Ensure the fabric is smooth and taut.
- Embroider as usual, taking care not to shift the fabric.
6.1.3 Tips for Successful Floating
- Use a sticky stabilizer for added security.
- For stretchy fabrics, consider using a temporary adhesive spray in conjunction with pins.
- Always test your method on scrap fabric before working on your final project.
By mastering the floating technique, you'll expand your embroidery capabilities and tackle projects that once seemed impossible. Remember, practice makes perfect, so don't be discouraged if your first attempts aren't flawless.
6.2 Using Fast Frames
Fast Frames are innovative hooping tools designed to streamline the embroidery process, especially for commercial embroiderers or those working on high-volume projects. These frames offer a quick and efficient alternative to traditional hooping methods.
6.2.1 Advantages of Fast Frames
- Significantly reduce hooping time
- Minimize fabric distortion and hoop burn
- Allow for easy repositioning and multiple placements
- Ideal for difficult-to-hoop items and bulky materials
6.2.2 How Fast Frames Work
- The frame consists of an outer frame and an inner plastic insert.
- Stabilizer is adhered to the plastic insert.
- The fabric is placed on top of the stabilizer and secured with temporary adhesive.
- The insert is then snapped into the outer frame, which attaches to the embroidery machine.
6.2.3 Best Practices for Using Fast Frames
- Always use high-quality stabilizer appropriate for your project.
- Ensure your fabric is smooth and wrinkle-free before attaching it to the frame.
- For bulky items, use the appropriate spacer to adjust the height of the frame.
- Clean the frames regularly to maintain their grip and effectiveness.
While Fast Frames can be a significant investment, they can dramatically increase productivity and consistency in your embroidery projects, making them an excellent choice for professionals and serious hobbyists alike.
6.3 Masking Fabrics
Masking is a clever technique used to protect delicate or pile fabrics from hoop burn and other embroidery-related damage. This method involves placing a protective layer between the fabric and the hoop or stabilizer.
6.3.1 When to Use Masking
- Embroidering on velvet, suede, or other pile fabrics
- Working with delicate materials like silk or satin
- Protecting finished garments from hoop marks
- Embroidering on items with a delicate surface texture
6.3.2 Masking Materials
- Water-soluble stabilizer (for most fabrics)
- Tear-away stabilizer (for sturdy fabrics)
- Tissue paper (for lightweight projects)
- Plastic wrap (for water-resistant fabrics)
6.3.3 Masking Technique
- Cut a piece of your chosen masking material slightly larger than your hoop.
- Place the masking material on top of your fabric.
- Hoop both the fabric and masking material together.
- Embroider your design as usual.
- After embroidery, carefully remove the masking material.
6.3.4 Tips for Effective Masking
- For pile fabrics, consider using two layers of water-soluble stabilizer.
- When using tissue paper, be prepared to pick out small pieces from the embroidery.
- Test your masking method on scrap fabric before committing to your final project.
Masking is an excellent technique to add to your embroidery toolkit, allowing you to work confidently on a wider range of fabrics and materials without fear of damage.
6.4 MaggieFrame's Innovative Magnetic Hooping System
In the world of embroidery, innovation is key to overcoming persistent challenges. Enter MaggieFrame's magnetic hooping system, a revolutionary approach that's changing the game for embroiderers of all levels.
6.4.1 The MaggieFrame Advantage
MaggieFrame's magnetic hoops offer several benefits over traditional hooping methods:
- Reduced Hoop Burn: The magnetic system distributes pressure evenly, significantly reducing the risk of hoop burn across various fabric types.
- Universal Compatibility: These hoops are designed to work with a wide range of industrial embroidery machines, making them a versatile choice for professionals.
- Time-Saving: The quick and easy hooping process can dramatically increase productivity, especially in high-volume settings.
- Gentle on Fabrics: The magnetic grip is firm yet gentle, making it ideal for delicate or challenging fabrics that are prone to damage with traditional hoops.
6.4.2 How MaggieFrame Works
- The system consists of two parts: a magnetic frame and a metal plate.
- Place your fabric and stabilizer on the metal plate.
- Position the magnetic frame over the fabric.
- The strong magnets securely hold the fabric in place without the need for tight clamping.
6.4.3 Best Practices for Using MaggieFrame
- Always use appropriate stabilizers for your project.
- Ensure your fabric is smooth and wrinkle-free before placing it on the metal plate.
- For extra security on slippery fabrics, consider using a light temporary adhesive spray.
- Take advantage of the quick-release feature for efficient multi-hooping on larger designs.
6.4.4 MaggieFrame for Challenging Projects
MaggieFrame excels in situations where traditional hoops struggle:
- Bulky Materials: The open design accommodates thick fabrics and multi-layered projects with ease.
- Delicate Fabrics: The gentle grip prevents damage to fine or easily marked materials.
- Stretchy Knits: The even pressure helps maintain fabric stability without distortion.
- Small or Awkwardly Shaped Items: The versatile system allows for creative positioning and secure hooping of challenging pieces.
By incorporating MaggieFrame's magnetic hooping system into your embroidery workflow, you're not just solving the problem of hoop burn – you're elevating your entire embroidery process. The system's efficiency, versatility, and fabric-friendly design make it an invaluable tool for both professional embroiderers and dedicated hobbyists looking to take their craft to the next level.
7. Best Practices for Machine Embroidery
7.1 Fabric and Design Selection
Choosing the right fabric and design is the foundation of successful machine embroidery. It's like selecting the perfect canvas and paint for a masterpiece - get it right, and you're halfway to creating something extraordinary.
7.1.1 Fabric Selection
When it comes to fabric selection, consider these factors:
-
Fabric Weight:
- Light fabrics (e.g., silk, organza) require lighter designs and careful stabilization.
- Medium-weight fabrics (e.g., cotton, linen) are versatile and work well with most designs.
- Heavy fabrics (e.g., denim, canvas) can support more complex, dense designs.
-
Fabric Stretch:
- Stretchy fabrics need extra stabilization to prevent distortion.
- Non-stretch fabrics are generally easier to embroider but may require different hooping techniques.
-
Fabric Texture:
- Smooth fabrics showcase intricate designs beautifully.
- Textured fabrics (e.g., terry cloth, velvet) may require simpler designs to prevent them from getting lost in the fabric's texture.
-
Fabric Color:
- Choose thread colors that contrast well with the fabric color.
- Consider using darker threads on lighter fabrics and vice versa for optimal visibility.
Pro Tip: When working with challenging fabrics, consider using MaggieFrame's magnetic embroidery hoops. Their gentle yet secure hold is particularly beneficial for delicate or stretchy materials, reducing the risk of fabric distortion and hoop burn.
7.1.2 Design Selection
Selecting the right design is crucial for achieving professional results:
-
Design Complexity:
- Match the design complexity to the fabric type and your skill level.
- Simple designs work well on textured fabrics, while intricate designs shine on smooth fabrics.
-
Stitch Count:
- Consider the fabric's strength when choosing designs with high stitch counts.
- Lightweight fabrics may pucker under dense designs.
-
Design Size:
- Ensure the design size is appropriate for the fabric and the item you're embroidering.
- Larger designs may require multi-hooping techniques.
-
Design Placement:
- Consider the item's purpose and shape when deciding on design placement.
- Use templates or positioning tools for accurate placement.
-
Thread Types:
- Choose thread types that complement both the fabric and the design.
- Consider using specialty threads for added dimension and interest.
Remember, the key to successful machine embroidery lies in the harmony between fabric and design. By carefully considering these factors, you'll set yourself up for embroidery success and minimize the risk of issues like hoop burn.
7.2 Proper Stabilizer Usage
Stabilizers are the unsung heroes of machine embroidery. They provide the necessary support to keep your fabric stable during the embroidery process, preventing distortion and ensuring crisp, clean designs. Let's dive into the world of stabilizers and learn how to use them effectively.
7.2.1 Types of Stabilizers
-
Cut-Away Stabilizer:
- Best for stretchy, knit fabrics
- Provides permanent support
- Ideal for designs with high stitch counts
-
Tear-Away Stabilizer:
- Suitable for stable, woven fabrics
- Easy to remove after embroidery
- Great for lightweight designs
-
Wash-Away Stabilizer:
- Perfect for delicate fabrics and items that require no visible stabilizer
- Dissolves in water
- Useful for free-standing lace designs
-
Heat-Away Stabilizer:
- Removes with the application of heat
- Ideal for fabrics that can't be washed or projects where tearing might damage the embroidery
-
Sticky Stabilizer:
- Has an adhesive surface to hold fabric in place
- Useful for hard-to-hoop items or when working with delicate fabrics
Pro Tip: When using MaggieFrame's magnetic hoops, you can often use a lighter weight stabilizer than you might with traditional hoops. The even tension provided by the magnetic system helps to stabilize the fabric, reducing the need for heavy-duty stabilizers in many cases.
7.2.2 Choosing the Right Stabilizer
Selecting the appropriate stabilizer depends on several factors:
-
Fabric Type:
- Stretchy fabrics usually need cut-away stabilizer
- Stable wovens can often use tear-away
- Delicate fabrics might require wash-away or heat-away stabilizers
-
Design Density:
- Dense designs need more stable support (cut-away or heavy tear-away)
- Light designs can often use lighter stabilizers
-
End Use of Item:
- Consider how the item will be used and cared for
- Items that will be washed frequently might need permanent stabilization
-
Visibility:
- For items where the back will be visible, choose stabilizers that can be completely removed or use matching colors
7.2.3 Layering Stabilizers
Sometimes, one layer of stabilizer isn't enough. Here's how to layer effectively:
- Hooped Layer: Start with a layer of cut-away or tear-away in the hoop
- Floated Layer: Add a layer of wash-away or tear-away on top for extra support
- Topping: For textured fabrics, use a water-soluble topping to prevent stitches from sinking
Remember, the goal is to provide enough support without making the embroidered area too stiff or bulky.
7.2.4 Stabilizer Application Techniques
-
Hooping with Stabilizer:
- Cut stabilizer larger than your hoop
- Hoop fabric and stabilizer together, ensuring both are taut but not stretched
-
Floating Technique:
- Hoop only the stabilizer
- Secure fabric to hooped stabilizer with temporary adhesive spray or pins
-
Basting:
- Use your machine's basting feature to secure fabric to stabilizer before embroidering
By mastering the art of stabilizer usage, you'll significantly improve the quality of your embroidery and reduce issues like puckering, distortion, and yes, even hoop burn. Remember, proper stabilization is key to achieving professional-looking results in machine embroidery.
7.3 Efficient Hooping Station Setup
Creating an efficient hooping station is like setting up a well-oiled machine - it streamlines your workflow, reduces errors, and ultimately leads to better embroidery results. Let's explore how to set up a hooping station that will make your embroidery process smoother and more enjoyable.
7.3.1 Choosing the Right Location
-
Ample Space:
- Ensure you have enough room to move freely around your hooping area
- Allow space for your embroidery machine, supplies, and works in progress
-
Good Lighting:
- Install bright, even lighting to reduce eye strain and improve accuracy
- Consider a daylight lamp for color-true illumination
-
Ergonomics:
- Set up your station at a comfortable height to prevent back strain
- Use an adjustable chair for proper posture during long embroidery sessions
7.3.2 Essential Tools for Efficient Hooping
-
Hooping Surface:
- Use a flat, sturdy table or a specialized hooping station
- Consider a non-slip mat to keep items in place
-
Hooping Aids:
- Invest in a variety of hoop sizes and styles
- Include specialty hoops for challenging items (e.g., caps, sleeves)
-
Marking Tools:
- Keep water-soluble marking pens and chalk nearby for design placement
- Include ruler and measuring tape for precise positioning
-
Scissors and Snips:
- Have sharp embroidery scissors for thread trimming
- Keep small, curved scissors for close trimming around designs
-
Stabilizer Station:
- Organize different types of stabilizers for easy access
- Use a stabilizer cutter for quick, clean cuts
-
Thread Organization:
- Use thread racks or drawers to keep colors organized and visible
- Consider color-coding your thread storage for efficiency
-
Hooping Accessories:
- Keep spray adhesive, target stickers, and placement rulers handy
- Include a variety of backing options for different fabric types
Pro Tip: Incorporate MaggieFrame's magnetic hoops into your hooping station setup. Their ease of use and quick release mechanism can significantly speed up your hooping process, especially when working on multiple projects or large batch orders.
7.3.3 Organizing Your Hooping Workflow
-
Pre-Hooping Preparation:
- Set up a staging area for items to be embroidered
- Pre-cut stabilizers to common hoop sizes
-
Hooping Zone:
- Designate a specific area for the actual hooping process
- Keep frequently used tools within arm's reach
-
Post-Hooping Area:
- Create a space for hooped items waiting to be embroidered
- Use a tiered system to manage multiple projects
-
Quality Control Station:
- Set up an area for inspecting finished embroidery
- Include good lighting and necessary tools for touch-ups
-
Finishing Area:
- Designate a space for trimming threads and removing stabilizers
- Include pressing equipment for final touches
7.3.4 Implementing Efficient Practices
-
Batch Similar Projects:
- Group projects that use the same hoop size or fabric type
- Minimize the need for frequent machine adjustments
-
Use Templates:
- Create reusable templates for common projects
- Speeds up placement and reduces errors
-
Maintenance Schedule:
- Set regular times for cleaning and organizing your station
- Keep tools sharp and in good condition
-
Digital Organization:
- Use software to manage designs and customer orders
- Implement a system for tracking project status
By setting up an efficient hooping station, you'll not only save time but also reduce the likelihood of errors that can lead to issues like hoop burn. A well-organized workspace allows you to focus on the creative aspects of embroidery, knowing that your technical setup is optimized for success.
7.4 Regular Machine Maintenance
Just as a car needs regular oil changes to run smoothly, your embroidery machine requires consistent maintenance to perform at its best. Proper care not only extends the life of your machine but also ensures high-quality embroidery results and minimizes issues like thread breaks, skipped stitches, and yes, even hoop burn. Let's dive into the essential practices for keeping your embroidery machine in top shape.
7.4.1 Daily Maintenance Routine
-
Cleaning:
- Remove lint and thread debris from the bobbin area and feed dogs
- Use a soft brush or vacuum attachment to clean hard-to-reach areas
- Wipe down the exterior of the machine to prevent dust accumulation
-
Needle Inspection:
- Check for bent or dull needles before each project
- Replace needles after 6-8 hours of use or when switching fabric types
-
Thread Path Check:
- Ensure thread is properly threaded through all guides
- Check for any snags or rough spots along the thread path
-
Tension Test:
- Perform a quick tension test on scrap fabric before starting a new project
- Adjust upper and lower tensions as needed
Pro Tip: When using MaggieFrame's magnetic hoops, regularly check the magnetic surfaces for any debris that might affect their performance. A clean magnetic surface ensures consistent tension across your fabric, reducing the risk of hoop burn and other embroidery issues.
7.4.2 Weekly Maintenance Tasks
-
Oil the Machine:
- Follow manufacturer's guidelines for oiling frequency and locations
- Use only machine-specific oil to prevent damage
-
Check and Tighten Screws:
- Inspect and tighten any loose screws, especially on the needle bar and presser foot
-
Clean the Bobbin Case:
- Remove the bobbin case and clean thoroughly
- Check for any nicks or burrs that could affect thread movement
-
Update Software:
- Check for and install any available software updates for your machine
7.4.3 Monthly Maintenance Checklist
-
Deep Cleaning:
- Perform a more thorough cleaning of all machine parts
- Pay special attention to areas prone to lint buildup
-
Hoop Inspection:
- Check all hoops for warping or damage
- Ensure screws and adjustment mechanisms are working properly
-
Calibration Check:
- Verify that your machine is properly calibrated
- Adjust if necessary, following manufacturer's instructions
-
Belt Inspection:
- Check drive belts for wear and proper tension
- Replace if showing signs of wear or damage
7.4.4 Annual Professional Service
-
Schedule Professional Maintenance:
- Have your machine serviced by a qualified technician at least once a year
- This helps catch potential issues before they become major problems
-
Timing Check:
- Have the hook timing verified and adjusted if necessary
- Proper timing is crucial for stitch quality and preventing thread breaks
-
Lubrication Service:
- Some parts may require professional lubrication
- This ensures all moving parts are working smoothly
-
Electrical Check:
- Have the machine's electrical components inspected for safety
- Ensure all connections are secure and functioning correctly
7.4.5 Maintenance Record Keeping
-
Maintenance Log:
- Keep a detailed log of all maintenance performed
- Include dates, tasks completed, and any parts replaced
-
Usage Tracking:
- Monitor machine usage hours to schedule timely maintenance
- Some machines have built-in counters for this purpose
-
Problem Documentation:
- Record any issues or unusual behavior you notice
- This can help identify patterns and prevent future problems
By following these maintenance practices, you'll not only extend the life of your embroidery machine but also ensure consistent, high-quality results. Regular maintenance reduces the risk of mechanical issues that can lead to problems like hoop burn, ensuring your embroidery projects turn out beautifully every time.
Remember, a well-maintained machine is a reliable partner in your embroidery journey. It allows you to focus on your creativity, knowing that your equipment is in top condition to bring your designs to life.
9. MaggieFrame: Revolutionizing Embroidery Hooping
9.1 Benefits of MaggieFrame Magnetic Embroidery Hoops
MaggieFrame magnetic embroidery hoops are not just another tool in your embroidery arsenal; they're a game-changer that's revolutionizing the way we approach hooping. Let's dive into the myriad benefits that make MaggieFrame stand out in the crowded world of embroidery equipment.
9.1.1 Effortless Hooping Process
Gone are the days of wrestling with traditional hoops and struggling to achieve the perfect tension. MaggieFrame's innovative magnetic system allows for quick and easy hooping, transforming what was once a time-consuming chore into a seamless process.
- Time-Saving: With MaggieFrame, you can hoop your fabric in seconds, drastically reducing setup time.
- Consistent Tension: The magnetic force ensures even tension across the fabric, eliminating the guesswork and inconsistencies of manual tightening.
- Reduced Physical Strain: Say goodbye to sore wrists and fingers from tightening hoop screws. MaggieFrame's design is ergonomically friendly, making it a boon for embroiderers who work long hours.
9.1.2 Superior Fabric Protection
One of the most significant advantages of MaggieFrame hoops is their gentle treatment of fabrics, especially delicate ones that are prone to hoop burn.
- Minimized Hoop Burn: The even distribution of pressure significantly reduces the risk of hoop burn, preserving the integrity of your fabric.
- Delicate Fabric Friendly: From silk to velvet, MaggieFrame handles delicate fabrics with care, allowing you to embroider on materials you might have hesitated to hoop traditionally.
- No Fabric Distortion: The magnetic grip holds fabric securely without stretching or warping, ensuring your embroidery design comes out exactly as intended.
9.1.3 Enhanced Embroidery Quality
The stability and precision offered by MaggieFrame hoops translate directly into improved embroidery quality.
- Reduced Registration Issues: The secure hold minimizes fabric shifting during embroidery, leading to more accurate stitch placement.
- Improved Stitch Quality: With consistent tension across the fabric, you'll notice an improvement in overall stitch quality and uniformity.
- Better Results on Challenging Fabrics: Even notoriously difficult fabrics like stretchy knits or slippery materials are held firmly in place, allowing for crisp, clean embroidery.
9.1.4 Versatility and Adaptability
MaggieFrame hoops are designed with versatility in mind, making them suitable for a wide range of embroidery projects and machines.
- Universal Compatibility: These hoops work with most major embroidery machine brands, offering flexibility in your setup.
- Multiple Size Options: From small, intricate designs to large, expansive projects, there's a MaggieFrame hoop size to suit your needs.
- Adaptable to Various Materials: Whether you're working with standard cotton, thick denim, or delicate organza, MaggieFrame hoops can handle it all.
9.1.5 Durability and Long-Term Value
Investing in MaggieFrame hoops is not just about immediate benefits; it's about long-term value for your embroidery business or hobby.
- Robust Construction: Built to withstand the rigors of frequent use, these hoops are a durable addition to your embroidery toolkit.
- Longevity: With no moving parts to wear out, MaggieFrame hoops outlast traditional hoops, offering excellent return on investment.
- Consistent Performance: The magnetic system maintains its strength over time, ensuring the same high-quality results project after project.
By incorporating MaggieFrame magnetic embroidery hoops into your workflow, you're not just upgrading your equipment – you're elevating your entire embroidery experience. From time savings and improved quality to fabric protection and versatility, these innovative hoops address many of the pain points embroiderers face daily. As we continue to explore MaggieFrame's offerings, you'll discover how these benefits translate into real-world applications, making your embroidery projects more enjoyable and your results more professional than ever before.
9.2 MaggieFrame Sizes and Compatibility
When it comes to embroidery, one size definitely does not fit all. That's why MaggieFrame offers a comprehensive range of hoop sizes to cater to every embroidery need, from small, intricate designs to large, statement pieces. Let's explore the variety of sizes available and their compatibility with different embroidery machines.
9.2.1 Available MaggieFrame Sizes
MaggieFrame understands that embroiderers work on a wide variety of projects, each requiring different hoop sizes. Here's a breakdown of the available sizes:
-
Small Hoops:
- 95x95 mm / 3.8x3.8 inch
- 130x130 mm / 5.1x5.1 inch
- 165x165 mm / 6.5x6.5 inch
- 175x175 mm / 6.9x6.9 inch
-
Medium Hoops:
- 150x205 mm / 5.9x8.1 inch
- 195x70 mm / 7.7x2.8 inch
- 215x225 mm / 8.5x9 inch
- 220x125 mm / 8.7x4.9 inch
- 240x240 mm / 9.5x9.5 inch
-
Large Hoops:
- 195x315 mm / 7.7x12.4 inch
- 265x315 mm / 10.5x12.4 inch
- 315x395 mm / 12.4x15.5 inch
-
Extra Large Hoops:
- 435x395 mm / 17.1x15.5 inch
-
Specialty Sizes:
- 100x325 mm / 4x12.8 inch
- 325x105 mm / 12.8x4.1 inch
It's important to note that the embroidery size is typically about 2cm smaller than the Hoop Inside Dimension, allowing for proper fabric tension and design placement.
9.2.2 Machine Compatibility
One of the standout features of MaggieFrame hoops is their universal compatibility. These innovative hoops are designed to work with a wide range of industrial embroidery machines, making them a versatile choice for embroidery professionals and enthusiasts alike. Here's a list of compatible machine brands:
- Brother (PR & VR series / Babylock)
- Tajima
- Happy
- SWF
- Ricoma
- Barudan
- ZSK
- Melco
- Janome
- Elna
- BAI
- Fuwei
- Yuemei
- Holiauma
- Feiya
- Promaker
- Fortever
- Yeshi
- Other Chinese brand machines
This extensive compatibility ensures that regardless of your machine brand, you can likely benefit from MaggieFrame's innovative hooping technology.
9.2.3 Choosing the Right Size
Selecting the appropriate hoop size is crucial for achieving the best embroidery results. Here are some tips to help you choose:
- Design Size: Always choose a hoop that's slightly larger than your design. This allows for proper stabilization and prevents distortion at the edges.
- Fabric Type: Consider the fabric you're working with. Larger hoops may be better for stretchy or delicate fabrics as they distribute tension more evenly.
- Project Type: For items like pockets or sleeves, smaller or specialty-sized hoops may be more appropriate.
- Machine Capacity: Ensure the hoop size you choose is compatible with your machine's embroidery field.
- Efficiency: For production work, choosing a hoop size that allows you to stitch multiple designs at once can significantly increase efficiency.
9.2.4 The Advantage of Multiple Sizes
Having access to various hoop sizes offers several benefits:
- Versatility: You can tackle a wide range of projects, from small logos to large jacket backs.
- Precision: Using the right-sized hoop for each project ensures better stitch quality and reduces the risk of fabric distortion.
- Efficiency: Matching hoop size to design size can speed up your workflow, especially for batch production.
- Fabric Economy: Proper hoop size selection can help minimize fabric waste, particularly when working with expensive materials.
9.2.5 Specialty Applications
MaggieFrame's range includes specialty sizes that cater to unique embroidery needs:
- Narrow Hoops: Ideal for embroidering on items like straps, belts, or narrow fabric strips.
- Extra Large Hoops: Perfect for large designs on jackets, quilts, or home decor items.
- Odd-Shaped Hoops: Designed for specific applications like embroidering on curved surfaces or in tight spaces.
By offering such a comprehensive range of sizes and ensuring compatibility with numerous machine brands, MaggieFrame provides a solution for virtually every embroidery challenge. Whether you're working on delicate handkerchiefs or large banner designs, there's a MaggieFrame hoop that's perfect for your project. This versatility, combined with the magnetic technology's benefits, makes MaggieFrame an indispensable tool in any modern embroidery setup.
9.3 Cost-Effectiveness and Durability of MaggieFrame Products
In the world of embroidery, where precision meets creativity, the tools you choose can make or break your projects. MaggieFrame magnetic embroidery hoops stand out not just for their innovative design, but also for their remarkable cost-effectiveness and durability. Let's delve into why these hoops are a smart investment for both professional embroiderers and enthusiastic hobbyists.
9.3.1 Initial Investment vs. Long-Term Savings
At first glance, the price tag of MaggieFrame hoops might seem higher than traditional embroidery hoops. However, this initial investment quickly translates into long-term savings:
- Reduced Fabric Waste: The precision and stability of MaggieFrame hoops significantly reduce the likelihood of misaligned or ruined embroideries, saving you money on wasted fabric and thread.
- Time Efficiency: Faster hooping and fewer re-hoops mean you can complete more projects in less time, increasing your productivity and potential earnings.
- Fewer Replacements: Unlike traditional hoops that wear out or break over time, MaggieFrame's durable construction ensures a longer lifespan, reducing the frequency of replacements.
9.3.2 Durability That Stands the Test of Time
MaggieFrame hoops are built to last, offering exceptional durability that sets them apart from conventional hoops:
- High-Quality Materials: Constructed with premium-grade materials, these hoops resist wear and tear even with frequent use.
- Corrosion-Resistant: The magnetic components are treated to prevent rust and corrosion, maintaining their strength and effectiveness over time.
- No Moving Parts: The absence of screws, springs, or other mechanical components eliminates common points of failure in traditional hoops.
9.3.3 Performance Consistency
One of the hallmarks of MaggieFrame hoops is their consistent performance over time:
- Magnetic Strength Retention: The high-quality magnets used in MaggieFrame hoops maintain their strength, ensuring reliable fabric tension project after project.
- Precision Alignment: The precise engineering of these hoops means they maintain their shape and alignment, delivering consistent results even after years of use.
9.3.4 Versatility Adds Value
The versatility of MaggieFrame hoops contributes significantly to their cost-effectiveness:
- Multi-Fabric Compatibility: From delicate silks to heavy denims, these hoops handle a wide range of fabrics, eliminating the need for multiple specialized hoops.
- Cross-Machine Usability: Their compatibility with various embroidery machine brands means you can use them even if you upgrade or change your machine.
9.3.5 Reduced Maintenance Costs
MaggieFrame hoops require minimal maintenance, further enhancing their cost-effectiveness:
- Easy Cleaning: A simple wipe-down is usually all that's needed to keep these hoops in top condition.
- No Lubrication Required: Unlike traditional hoops with moving parts that need regular lubrication, MaggieFrame hoops operate smoothly without additional maintenance.
9.3.6 Environmental and Economic Sustainability
The durability of MaggieFrame hoops also contributes to environmental sustainability:
- Reduced Waste: Fewer replacements mean less waste in landfills.
- Energy Efficiency: The ease of use and efficiency of these hoops can lead to reduced energy consumption in your embroidery projects.
9.3.7 Customer Testimonials
Don't just take our word for it. Here's what some MaggieFrame users have to say:
"I was skeptical about the price at first, but after a year of heavy use, my MaggieFrame hoops look and perform like new. They've paid for themselves many times over in time saved and improved quality." - Sarah, Professional Embroiderer
"As a hobbyist, I appreciate how these hoops have made my projects easier and more enjoyable. The fact that I haven't had to replace them in three years is a bonus!" - Mike, Embroidery Enthusiast
9.3.8 Warranty and Support
MaggieFrame stands behind their products with:
- A comprehensive warranty covering manufacturing defects
- Responsive customer support to address any issues or questions
In conclusion, while MaggieFrame magnetic embroidery hoops may require a higher upfront investment, their durability, consistent performance, and time-saving features make them a cost-effective choice in the long run. By reducing fabric waste, increasing productivity, and requiring fewer replacements, these hoops offer excellent value for money. Whether you're running a busy embroidery business or pursuing embroidery as a passionate hobby, MaggieFrame hoops are an investment that pays dividends in quality, efficiency, and satisfaction project after project.
10. Frequently Asked Questions About Hoop Burn and Magnetic Hoops
10.1 What causes hoop burn in embroidery?
Hoop burn is primarily caused by excessive pressure and friction when fabric is tightly secured in an embroidery hoop. The compression of fabric fibers, combined with the heat generated during the embroidery process, can lead to visible marks or indentations on the fabric. Factors contributing to hoop burn include:
- Over-tightening the hoop
- Using an incorrectly sized hoop for the project
- Leaving fabric in the hoop for extended periods
- Working with delicate or pile fabrics without proper protection
- Heat and moisture from the embroidery process
10.2 Can hoop burn be prevented entirely?
While it's challenging to prevent hoop burn entirely, especially when working with sensitive fabrics, there are several effective strategies to minimize its occurrence:
- Use proper hooping techniques, avoiding over-tightening
- Select the appropriate hoop size for your project
- Utilize floating techniques for delicate fabrics
- Employ stabilizers and backing materials effectively
- Consider using magnetic hoops, like MaggieFrame, which distribute pressure more evenly
MaggieFrame's magnetic embroidery hoops offer a significant advantage in preventing hoop burn. Their innovative design provides consistent tension across the fabric without the need for excessive tightening, making them an excellent choice for both professionals and hobbyists concerned about fabric damage.
10.3 Are certain fabrics more prone to hoop burn?
Yes, some fabrics are more susceptible to hoop burn than others:
- Delicate fabrics: Silk, satin, and organza
- Pile fabrics: Velvet, corduroy, and chenille
- Stretchy fabrics: Knits and jersey materials
- Napped fabrics: Fleece and terry cloth
- Synthetic fabrics: Polyester and nylon blends
When working with these fabrics, extra precautions are necessary. MaggieFrame's magnetic hoops are particularly useful for these challenging materials, as they provide a secure hold without excessive pressure on the fabric fibers.
10.4 How do magnetic hoops differ from traditional hoops?
Magnetic hoops, such as those offered by MaggieFrame, differ from traditional hoops in several key ways:
- Pressure distribution: Magnetic hoops provide even pressure across the fabric, reducing the risk of hoop burn.
- Ease of use: They allow for quick and easy hooping, saving time and reducing physical strain.
- Versatility: Magnetic hoops can handle a wide range of fabric types, from delicate silks to heavy denims.
- Stability: They offer superior fabric stability during the embroidery process, improving stitch quality.
- Rehooping: Magnetic hoops make it easier to rehoop large designs or multiple placements accurately.
MaggieFrame's magnetic hoops are designed to be compatible with a wide range of industrial embroidery machines, making them a versatile choice for embroidery businesses of all sizes.
10.5 Can hoop burn be removed after it occurs?
In many cases, hoop burn can be reduced or removed after it occurs. The effectiveness of removal methods depends on the severity of the burn and the type of fabric. Here are some techniques to try:
- Steaming: Gently steam the affected area to help relax the fibers.
- Water spraying: Lightly mist the area with water and allow it to air dry.
- Fabric brushing: Use a soft-bristled brush to gently lift compressed fibers.
- Lint roller: For pile fabrics, a lint roller can help restore the nap.
- Laundering: For washable items, a gentle wash cycle can often remove hoop burn.
Remember to always test these methods on an inconspicuous area first, especially with delicate or valuable items.
10.6 Are magnetic hoops suitable for all embroidery machines?
While magnetic hoops offer many advantages, their compatibility can vary depending on the embroidery machine model. MaggieFrame has designed their magnetic hoops to be compatible with a wide range of industrial embroidery machines, including popular brands such as:
- Brother (PR & VR series / Babylock)
- Tajima
- Happy
- SWF
- Ricoma
- Barudan
- ZSK
- Melco
- Janome
- And many others
Before investing in magnetic hoops, it's essential to check compatibility with your specific machine model. MaggieFrame's customer support can assist in determining the right hoop for your equipment.
10.7 How do I choose the right size magnetic hoop for my project?
Selecting the correct size magnetic hoop is crucial for achieving the best embroidery results. Consider the following factors:
- Design size: Choose a hoop slightly larger than your embroidery design.
- Fabric type: Larger hoops may be better for stretchy or delicate fabrics.
- Machine capacity: Ensure the hoop size is compatible with your machine's embroidery field.
- Project type: Consider specialty sizes for items like caps or sleeves.
MaggieFrame offers a range of hoop sizes to accommodate various project needs, from small 95x95mm hoops to large 435x395mm options.
10.8 Are magnetic hoops safe to use with all fabrics?
Magnetic hoops are generally safe for most fabrics, but there are a few considerations:
- Delicate fabrics: Use with caution and consider adding a layer of stabilizer for extra protection.
- Metallic fabrics: Test a small area first to ensure the magnets don't affect the fabric's appearance.
- Very thick materials: Check that the magnetic force is strong enough to hold securely.
MaggieFrame's hoops are designed to work with a wide range of fabric types, from delicate silks to heavy denims, making them a versatile choice for various embroidery projects.
10.9 How do I maintain my magnetic hoops?
Proper maintenance of magnetic hoops is essential for their longevity and performance:
- Clean the magnetic surfaces regularly with a soft, dry cloth.
- Store hoops in a dry place to prevent rust or corrosion.
- Keep magnetic surfaces free from debris that could interfere with fabric placement.
- Avoid dropping or mishandling the hoops, as this could affect magnet alignment.
- Periodically check for any loose components and tighten if necessary.
MaggieFrame's magnetic hoops are built to last, but proper care will ensure they continue to perform optimally for years to come.
10.10 Can magnetic hoops improve embroidery quality?
Yes, magnetic hoops can significantly improve embroidery quality in several ways:
- Reduced fabric distortion: Even pressure distribution minimizes stretching and puckering.
- Improved stitch consistency: Stable fabric tension leads to more uniform stitches.
- Better registration: Accurate hooping ensures design elements align correctly.
- Fewer thread breaks: Stable fabric reduces stress on threads during stitching.
- Enhanced detail work: Precise tension control allows for intricate designs on various fabrics.
MaggieFrame's magnetic hoops are designed to address these quality concerns, helping embroiderers achieve professional results consistently across a wide range of projects.
11. Conclusion
As we wrap up our deep dive into the world of hoop burn in machine embroidery, it's clear that this common challenge is far from insurmountable. Armed with the knowledge and techniques we've explored, from prevention strategies to removal methods, you're now equipped to tackle hoop burn head-on. Remember, the key lies in understanding your fabrics, mastering proper hooping techniques, and leveraging innovative solutions like MaggieFrame's magnetic hoops. By implementing these best practices, you'll not only prevent hoop burn but also elevate the overall quality of your embroidery projects. Embrace these insights, experiment with different approaches, and watch as your embroidery skills flourish, producing flawless, professional results time after time.